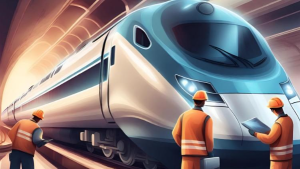
How does the rail industry organise its activities?
The rail industry has a particular focus on customer service due to the massive and complex system that applies to it. These complex systems give an advantage to the manufacturer to propose a service to support their system. At a time when most governments around the world prioritize a friendly ecological transport system and invest more in rail projects, The service business of the rail industry has a promising future, particularly in the EU where public rail monopolies will give way to open competition. (See this article of the European Commission).
To excel in service delivery, it’s essential to first establish a robust support system that enables efficient management of your assets.
First, let’s outline how major manufacturers organise their business units to fulfil customer contracts.
The major manufacturers of the rail industry split globally their activities into 4 businesses.
- Deliver rolling stock for the need of new or existing lines.
- Build and install complex signalling systems on new lines or existing lines.
- Deliver install and manage proper infrastructure and system interface for new lines.
- Provide services to clients on all different types of rail equipment.
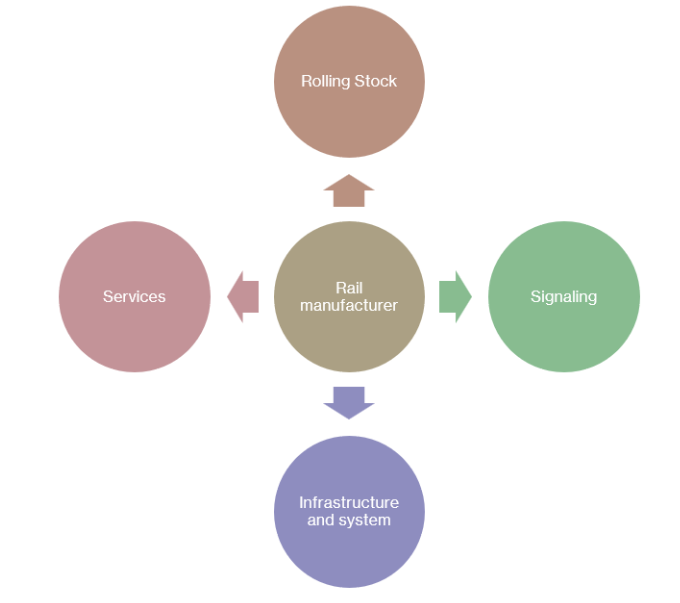
My previous experience as an LSA engineer and ILS manager for rolling stock and signalling systems showed me how ILS applies to these different activities and the difference between them. ILS is the premise of the operation phase of your project that means to optimise the profit from their new system customer will ask the better for their ILS deliverable.
What system characteristics does ILS impact?
Safety, availability and operation cost are 3 values that ILS has a big role in. These three values are usually the reason for the improvement projects of the railway systems.
It’s unsurprising that as rail systems become increasingly automated, they must address heightened safety concerns during their operation.
Not surprising when we know how much the operator is challenged on the availability of the system.
Not a surprise at all when we know that 70% of the cost of Rail equipment is spent during the operation period.
These 3 values are treated during your ILS process, starting from design to be able to easily maintain the system during the lifespan but also design the necessary support system to optimise your asset management activities.
Equipment maintained correctly limits the risk of major failure that can increase the risk of safety for operators and users.
Having your system reliable and well-maintained means that your system will be operational and available when it’s needed.
By optimizing your maintenance activities and maximizing equipment availability, ILS helps your system reduce your life cycle cost.
Now that the importance of ILS in the rail industry has been brought back, let’s have a view of 4 lessons from my experience, that every ILS organization needs to consider avoiding some of the issues very common during a project.
The aim is not to provide a comprehensive manual for ILS but rather to highlight key points often overlooked by ILS organisations when working on a project.
Four key lessons that I’ve learned during my time in the rail industry
The four points are:
- Establish robust processes
- Focus on requirements
- Manage suppliers
- Be flexible
1. Establish robust processes
The rail industries follow a development process for their final products that closely resemble that of the automotive industry.
This development process works on 3 different layers:
- Development of products that will be used for future/current platforms.
- Development of platforms that will be used as a base for the future project.
- Project development will be the last development before delivering the system to the customers.
This organisation’s purpose is to streamline project delivery by mutualising products across platforms. Platforms are designed to support project delivery, to minimise the need for project-specific development wherever possible. In Addition to these products platforms and projects can be composed of COTS (commercial off-the-shelf) equipment.
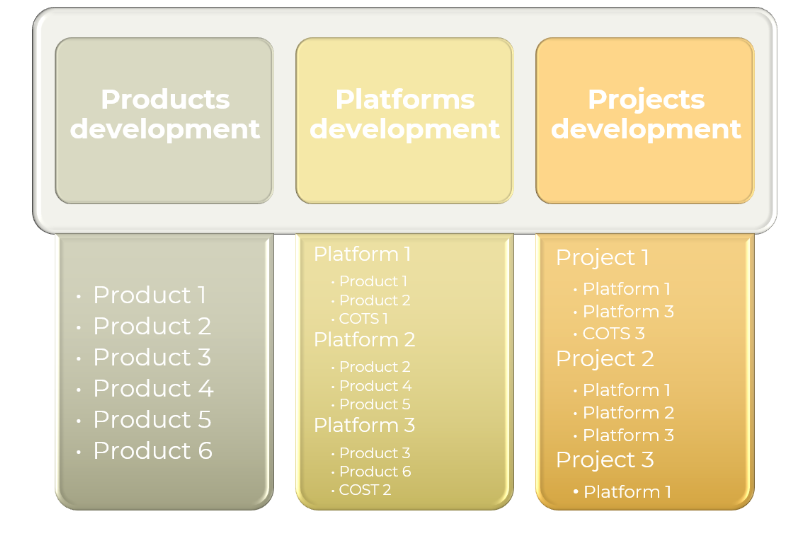
This point is very important, thinking of how to support the system from the first step of the design of the solution can avoid some unsolvable problems, and increase the efficiency of the ILS deliveries during the project.
Neglecting the importance of having a proper ILS following from day one will lead to a blocking point because your system will not be sustainable.
2. Focus on requirements
An often-overlooked aspect during both the tender phase and project execution is the thorough analysis of requirements and devising appropriate responses to address them.
You can find Kirstie’s article, Moving Away from the Omniscience of Project Managers – the Road of the Business Analyst and Their Toolkit, Less Travelled…
Industrials typically conduct their requirement analysis diligently during the tender phase. However, adequately addressing non-standard requirements is often overlooked during both the tender process and the initial stages of the project. Consequently, when clients inquire about responses to these non-standard requirements, it can present challenges as they were not adequately planned or quoted for.
The tendency is to consider that the ILS package delivery will be the same for all the projects, so negligence happens often during the tender phase due to not considering the gap between the usual work package and what the customer wants, especially for the quotation of the ILS activities.
To avoid that is important to link your requirement to a deliverable to be sure that the proper amount of time and money will be available to conduct your project. The sooner, the better, that means if this work can be done during the tender that will limit the risk of getting wrong with the quotation.
It’s also important to share with your client how you are going to respond to your requirement to have their acknowledgement and avoid any rework.
For that, you must know what your usual work package is to be able to analyze the gap between requirements and your abilities as an ILS team.
The second step that is very important is how to bring this different contract requirement to the development of a new product and the development of the supportability system that goes with it.
The unusual requirement for your usual work package needs a deeper analysis, to understand if it’s just a one-time thing (that can be subcontracted easily) or if it’s a real tendency. If this is the case, it will be important to report this requirement to all the different layers of development to be sure that the need is correctly addressed.
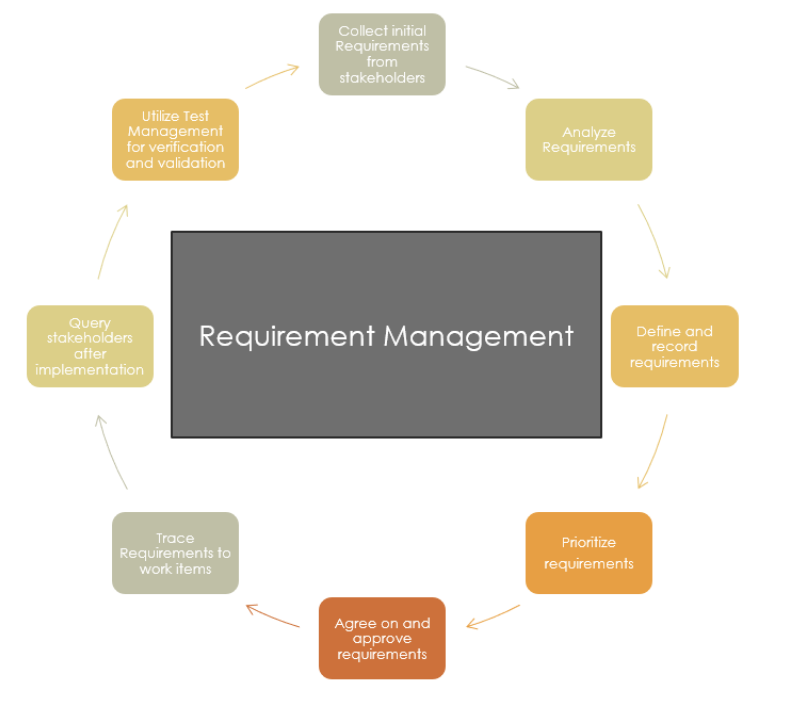
3. Manage suppliers
Supplier management is frequently disregarded concerning ILS, yet it holds paramount importance in acquiring the necessary product information at the appropriate level and format. This ensures efficiency and minimises the need for rework on deliveries from suppliers.
The keys here are:
- To have the contract that requires your supplier to provide the necessary elements in the best format.
- Settle with your suppliers is a good way to follow all the work. Having weekly reviews to have a view of how the work advances and be able to guide them when it’s necessary.
For that is important to define as soon as possible the need and the format to avoid rework and possible contractual issues with your supplier.
Also, it is very important to make sure that your supplier has the level of transparency and the necessary skills to provide support to your product.
To finish, you should always open a door for change with your supplier. And alert them as soon as a change happens that can have an impact on the deliveries of your supplier.
4. Be flexible
The specificity of the rail industry is the number of customers and operators/maintainers all around the world. This particularity forces suppliers to be flexible in terms of ILS deliverables. The fact that the different entities have different organizations, skills and HR management brings difficulties to use generic Logistics support analysis (LSA)studies for all the projects.
Unlike in the defence industry when the number of end users is less important than in the rail industry and the facts that strong standards used by the defence industry force all the stakeholders to have a more restricted way to display the ILS deliverable.
In addition to design changes throughout the project, there are also variations in orders contracted with the client or new stakeholders introduced, particularly evident in turnkey projects where the operator/maintainer is specified during the design and build (D&B) contract phase. Flexibility becomes the essential factor enabling efficient responses to meet all client needs.
A good flexibility needs:
- Maintaining consistent communication with your client to gain insight into their perspective and achieve a thorough understanding of their needs.
- Continuous communication with the departments engaged in the project is crucial for being responsive to changes and understanding how they may affect your Integrated Logistics Support (ILS) activities.
- You need to think of your ILS activities as a strategy, focus on what is your deliverable and how are you going to deliver it with the best efficiency. It’s very important to have a precise vision of how you will conduct your project and link your strategy to your planning, the project planning, the milestones and to finish the resources that you have.
A certain number of parameters and choices can be taken into consideration:
-
Requirement analysis to understand the scope, the deliverable and the best format (See above).
- Design analysis to have a good view of the system.
- Try to find an older project that you can use as a reference to limit the rework.
- Have a gap analysis between your future deliverables and the deliverables of older projects available.
- Based on that create your list of activities
- Link this list to your deliverable, your planning, the project planning and milestones and your resources.
- Define the necessary input that you need and share all the information with the project.
- Share your template and your deliverable with your client to be aligned with them before starting to produce.
These different points will help you to have a clear path to follow but also to be able to have the change information as soon as possible. Because you detailed your activities, your deliverables and your planning, you will easily see what the impact on your activities, deliverables and planning will be and be efficient in responding and communicating about this change.
In a few words, the more prepared you are, the more you will be able to be flexible when change happens in your projects.
Conclusion
To conclude, a lot of other parameters need to be taken into consideration to be successful in your ILS activities. But these 4 topics will probably help you to be more efficient with your ILS deliveries and enable better supportability on your system.
ILS which is basically a management discipline to enable correctly the support of a system, needs to be recognized as part of the system engineering to be completely successful.
It’s crucial to understand that ILS organizations need continuous improvement and to reinvent themselves through new management and communication techniques, new tools and new skills. The implementation of new technologies, like virtualization, cybersecurity, the cloud, data management etc. will also force the ILS engineer to be constantly trained in these new technologies.
If you were to implement the four lessons, what impact might that deliver for your next project?
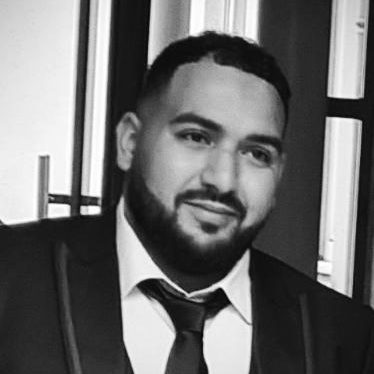
About the Author
Hassen Nedhif is a support solution expert, having over 9 years of experience in the ILS discipline in multiple positions, mostly in the rail sector for both rolling stock and signalling projects.
Connect with Hassen on LinkedIn
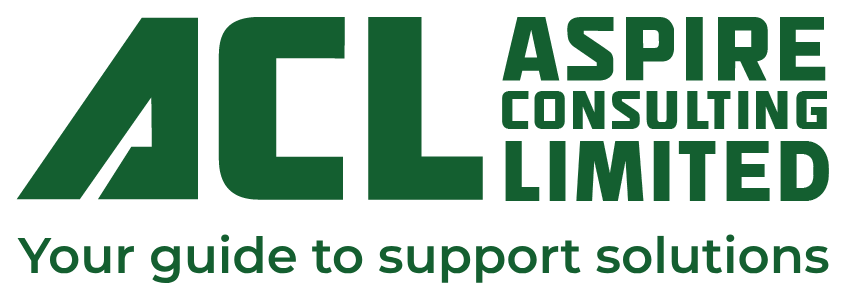
About Aspire
What does Aspire do? Almost every organisation on the planet uses equipment to deliver its service. Very few are always
happy with the performance of that equipment. We train, guide and
collaborate with organisations to design support solutions that keep
equipment performing, so they can deliver their service, consistently and
effectively.
Follow Aspire on LinkedIn